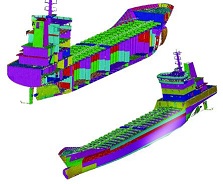
隨著造船工業(yè)的發(fā)展,柴油機尺寸越來越大,使得曲軸的工作條件愈來愈惡劣,曲軸的強度計算是柴油機設計中的一個關鍵問題。如何得到準確的曲軸應力分布、固有頻率和模態(tài)振型,對改善其結構設計具有重要的理論意義。此外,在航行中可能會出現由于船體變形等原因造成較大的船舶應力和附加彎曲應力。突變的扭轉振動會影響船舶柴油機曲軸的扭轉應力,導致曲軸最終的疲勞斷裂。本文以船舶柴油機整個系統(tǒng)為研究對象,結合AVLEXCITE多體動力學與ANSYS的有限元分析法對船舶柴油機額定工況下曲軸進行動態(tài)特性分析,充分考慮整個船舶柴油機各個部件間的相互作用,即克服傳統(tǒng)算法中邊界條件不夠準確的弊端,深入考慮曲軸上油孔和圓角等細小結構,使模型的精確性更加接近曲軸在工作狀態(tài)中的實際條件。
AVLEXCITE多體動力學中用3個坐標系來構建系統(tǒng)模型:①全局坐標系(X,Y,Z),用于描述各彈性體在系統(tǒng)中的全局運動,此坐標系為靜止坐標系;②隨動坐標系(X',Y',Z'),即隨各體一起運動;③子坐標系(X″,Y″,Z″),即子結構ai的坐標系。圖為系統(tǒng)中彈性體子結構的模型。子結構ai承受內力、外力及內、外力矩的作用,子結構的運動服從動量和角動量定理。
應用上述數學模型,建立船舶柴油機系統(tǒng)模型進行多體動力學數值分析。將彈性體的作用力/形變作為連接體進行流體動力學分析的邊界條件,而連接體的力矩/作用力成為彈性體的約束力矩/力,進行迭代計算,有效地解決了彈性體與連接體間的耦合問題。
在有限元軟件ANSYS中建立曲軸和主軸承的實體有限元模型,各個模型均采用solid45六面體單元,并在模型中接觸位置定義主自由度節(jié)點,通過縮減程序把大幅度的自由度進行壓縮,從而大大縮小了模型計算的規(guī)模,但是計算結果過程中的精度卻沒有受到太多影響。經過縮減獲得子結構各項參數文件:主自由度文件、幾何文件、質量和剛度矩陣、個體(剛度)矩陣等信息。圖為定義過主自由度的船舶主軸承和曲軸有沖程、轉速127r/min、發(fā)火順序1-6-2-4-3-5、缸數6、缸徑500mm、氣體壓力等,該系統(tǒng)模型坐標系應與有限元模型坐標系保持一致。將縮減后的船舶主軸承和船舶曲軸的模型導入動力學軟件AVLEXCITE中,并在EXCITE中對體單元和連接單元進行定義考慮本文研究目標,模型中建立缸套的剛體模型,并建立空間固定點;連桿僅采用3節(jié)點模型。各結構體之間通過活塞與缸套導向、各種軸承等連接體建立非線性耦合關系。模型中,用軸向均布5排,并且每排均布48根非線性彈簧來模擬各個主軸承,見圖。各根彈簧定義的阻尼和剛度值參照軸承潤滑油膜的阻尼特性和剛度特性。
氣體力載荷施加在連桿小端質量節(jié)點處。圖是氣體力曲線,描述柴油機轉速在127r/min,氣體爆發(fā)壓力峰值為15.2MPa時,氣缸壓力隨曲軸轉角的變化規(guī)律。整個柴油機系統(tǒng)多體動力學模型見圖。
在Pro/E中建立精細的三維船舶曲軸實體模型,并將其導入ANSYS進行有限元動應力恢復計算。模型考慮了船舶曲軸上細小結構,例如:油孔、過渡圓角等。在模型整體網格劃分后,又將網格進一步細化來減小由于網格劃分造成的計算誤差。
由圖可以看出,在軸頸的過渡圓角處各曲拐均出現了最大應力,這是因為不管是在主軸頸過渡圓角或是連桿頸過渡圓角,局部結構尺寸均比較小,應力集中更加嚴重。因為曲軸輸出端因帶外部負載而導致自身載荷較大,造成從自由端到輸出端,過渡圓角處應力值有增大的趨勢。
1)通過多體動力學和三維實體有限元結合的方法對船舶曲軸進行動態(tài)特性計算,結果表明在柴油機額定工況下,各曲拐最大應力均發(fā)生在各軸頸過渡圓角處,且計算精度更加精確;
2)本文建立了整體船舶柴油機多體動力學模型,克服了單體模型計算分析時邊界載荷條件不夠準確的弊端。更精確地分析了船舶曲軸在運轉工況下的動態(tài)力學響應特性,也更符合船舶曲軸工作時的實際條件。
專業(yè)從事機械產品設計│有限元分析│強度分析│結構優(yōu)化│技術服務與解決方案
杭州那泰科技有限公司
本文出自杭州那泰科技有限公司dbzq999.cn,轉載請注明出處和相關鏈接!